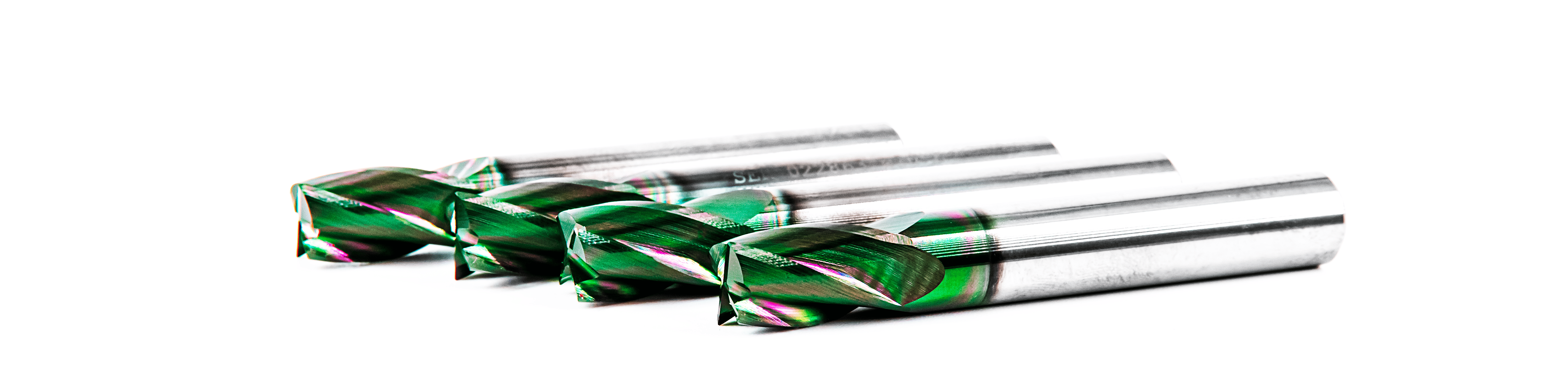
Os revestimentos PVD são aplicados na superfície de componentes para proteger os componentes contra contra o desgaste, corrosão, oxidação, etc, sob condições severas de uso; ao mesmo tempo que conferem aos componentes um aspeto atraente/brilhante.
A tecnologia de revestimento PVD (Deposição Física em fase de Vapor) é um processo em que os metais são convertidos em fase gasosa e transferidos para o componentes a revestir, formando um revestimento fino. Estes revestimentos têm uma espessura de alguns microns (um décimo da espessura de um cabelo), no entanto, melhoram significativamente as propriedades dos componentes. A resistência ao desgaste é aumentada até 20 vezes. Os componentes são protegidos contra o desgaste, corrosão, oxidação a altas temperaturas e ficam com um aspeto atraente.
A nossa tecnologia
Para produção dos revestimentos, utilizamos a tecnologia de pulverização catódica - PVD, incluindo a pulverização catódica de magnetrão DC, pulsada, e a pulverização catódica de Impulsos de alta potência- HiPIMS.
Todos os materiais metálicos, exceto materiais com zinco, vidro, plásticos e cerâmicos podem ser revestidos. Para o revestimento de peças e ferramentas, estamos limitados ao tamanho da câmara de vácuo, podendo revestir componentes com dimensão máxima de diâmetro de 450 mm e altura de 700 mm. Para algumas aplicações decorativas, podemos revestir peças até um diàmetro máximo de 1300 mm e 1500 mm de altura.
É possível depositar revestimentos a baixas temperaturas (até 150°C) para que as propriedades do material de base ao qual o revestimento é aplicado (por exemplo, alumínio, aço, etc) não seja alterado pela temperatura.
Como é que a tecnologia PVD funciona?
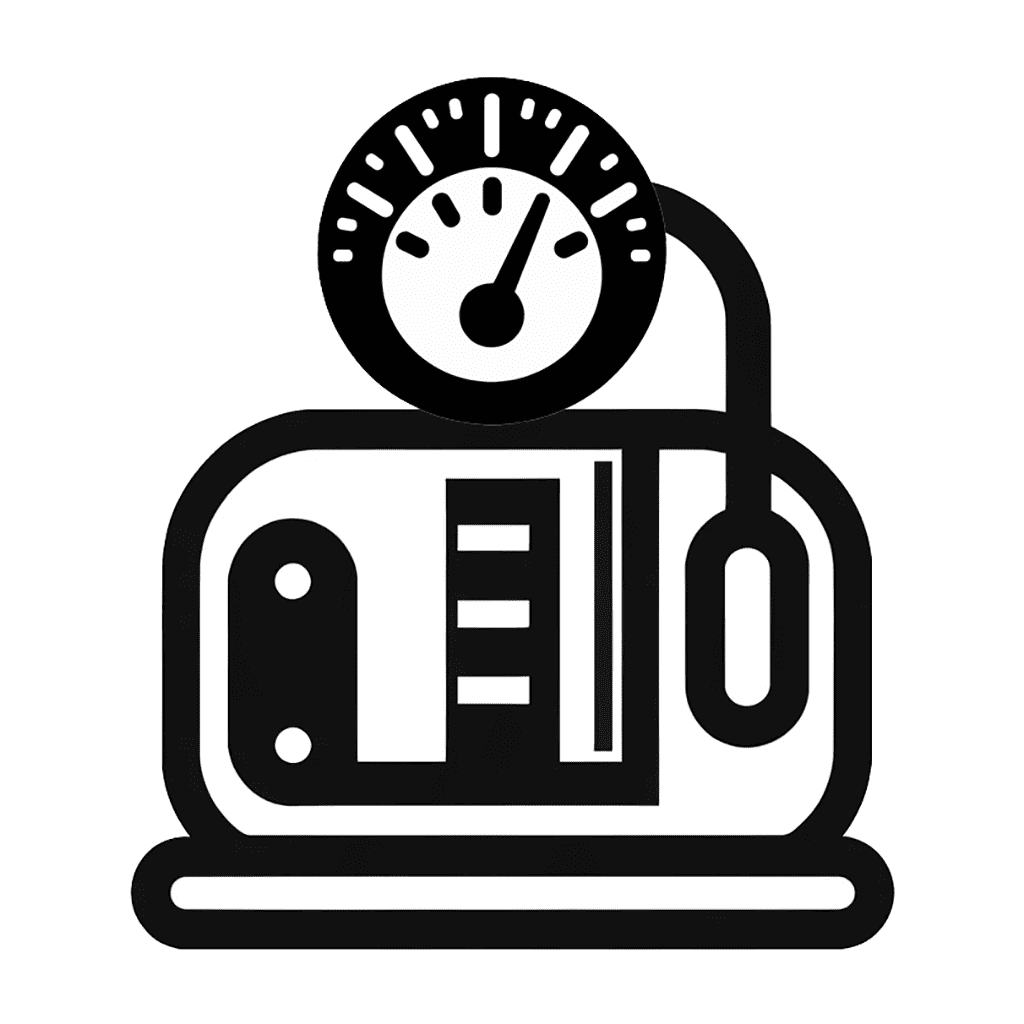
Vaccum na câmara
10 – 30 min
O componente é colocado dentro da câmara de deposição, que é então evacuada até atingir uma pressão muito baixa. Este passo assegura que o processo de revestimento ocorre num ambiente sem ar ou outros gases indesejáveis que afetam a qualidade do revestimento.
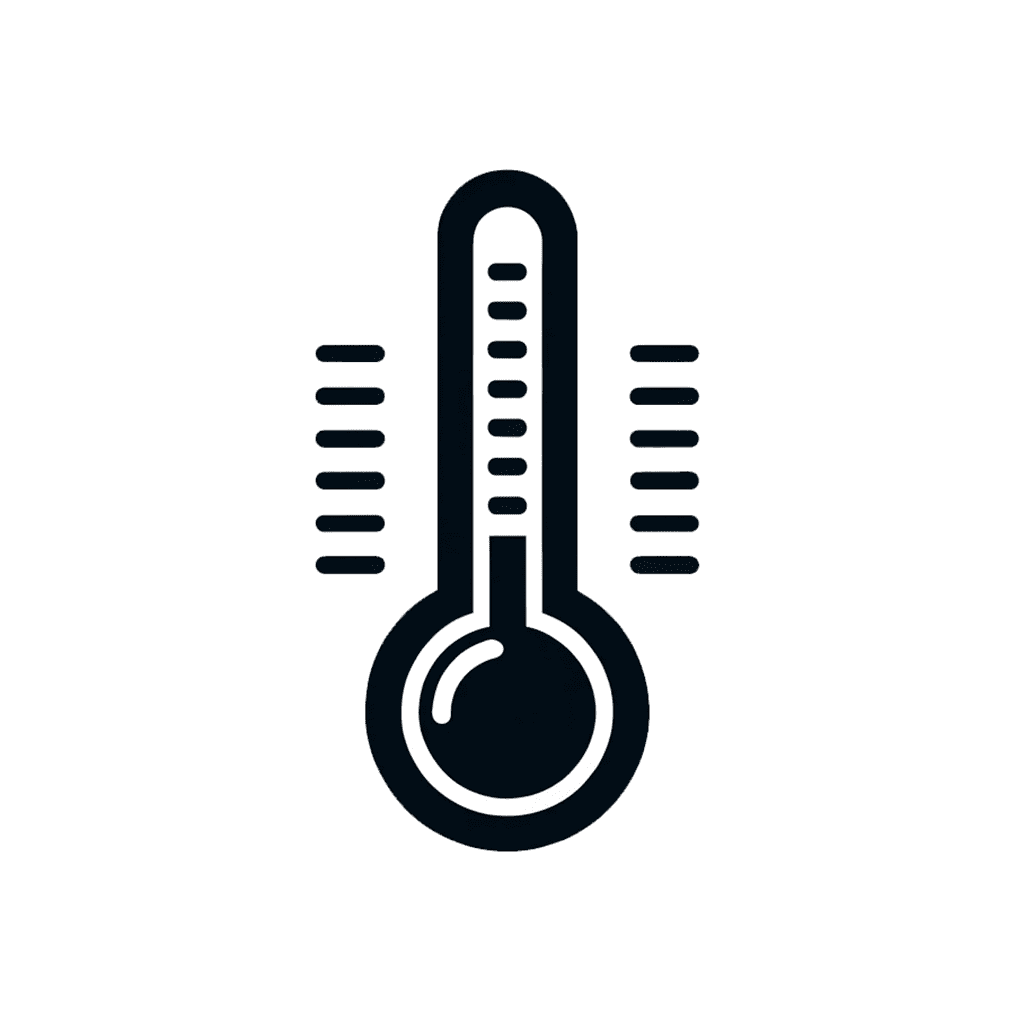
Aquecimento
90 min
A câmara de deposição é aquecida para melhorar a adesão e a densidade do revestimento. A temperatura e o tempo de aquecimento dependem do material do componente e das propriedades desejadas do revestimento, situando-se normalmente entre 180-450 °C.
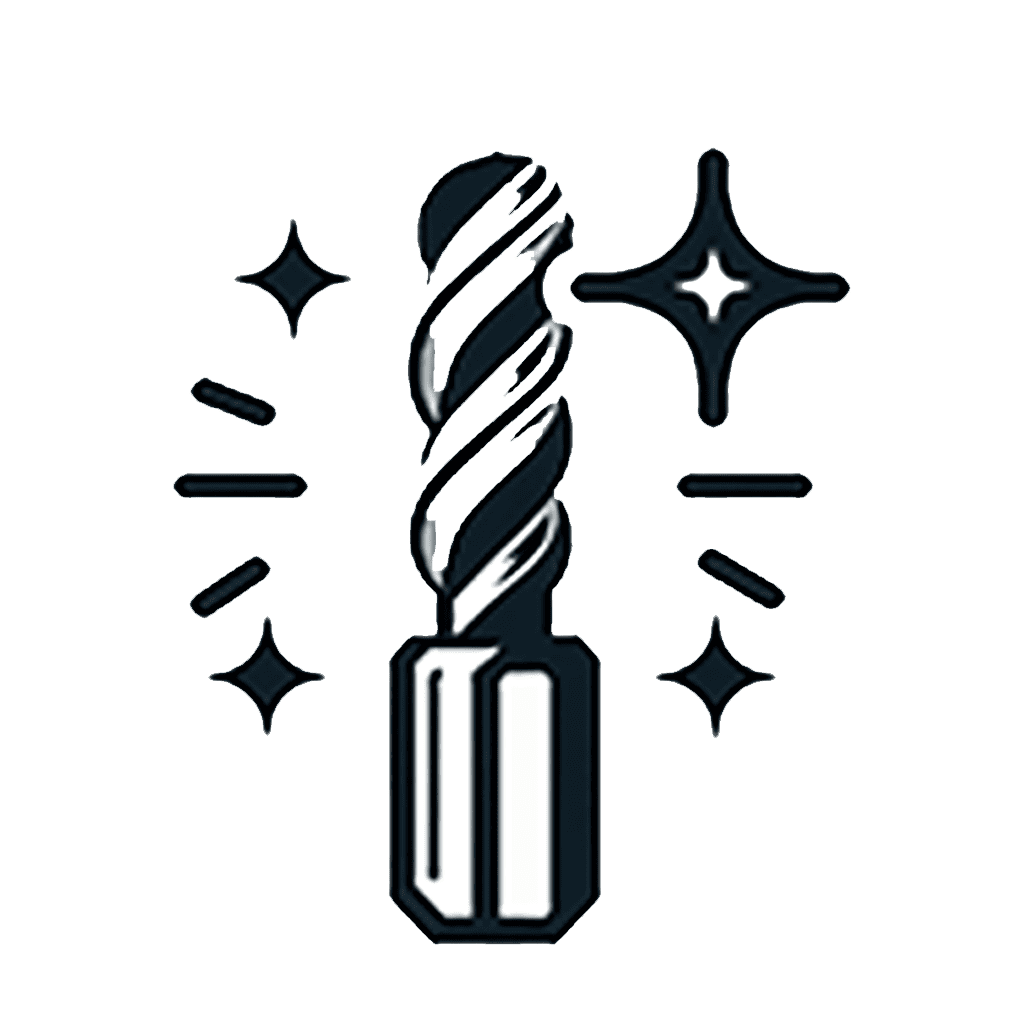
Limpeza iónica
30 – 90 min
A limpeza por bombardeamento de iões remove a camada fina de óxido que se forma na superfície das peças metálicas. Isto aumenta a adesão do revestimento ao substrato e resistência ao desgaste. A limpeza iónica ativa a superfície das peças.

Revestimento
2 – 10 hod
O material de revestimento (titânio, zircónio, alumínio, etc.) é vaporizado na câmara de deposição e deposita-se diretamente no componente, formando uma película fina. Os parâmetros são ajustados para assegurar a espessura e propriedades desejadas do revestimento.
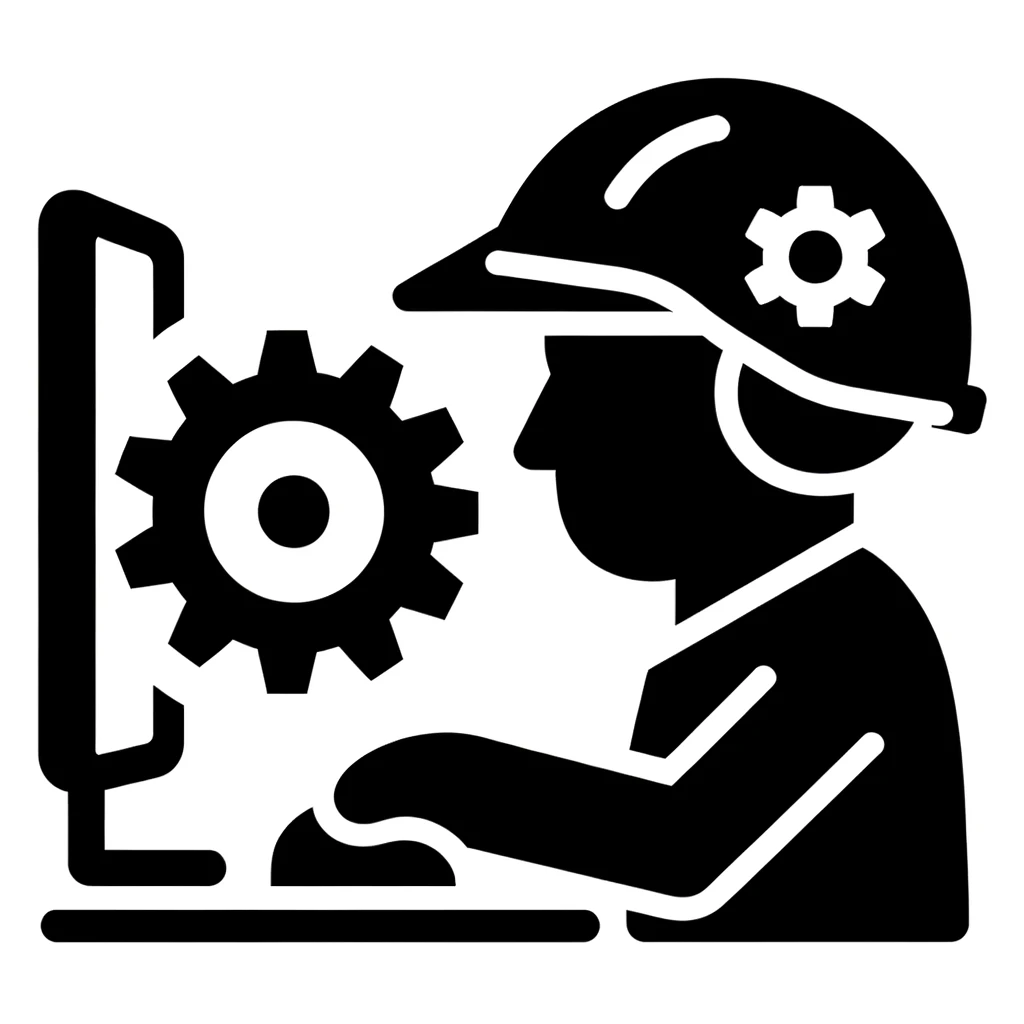
Controlo de qualidade
12 hod
Após o processo, a câmara é aberta à pressão atmosférica e a peça é arrefece. Segue-se uma avaliação de qualidade, incluindo medição da espessura dos revestimentos e avaliação da adesão, para assegurar as propriedades desejadas.
Existem uma grande variedade de revestimentos disponíveis no nosso portefolio e estamos aqui para o ajudar a escolher a solução certa para as suas necessidades. Para os clientes que têm necessitem de revestimentos com bom aspeto visual, temos revestimentos decorativos depositados por HiPIMS. Os clientes que necessitem de reduzir o atrito no seu processo de fabrico ficaram satisfeitos com os revestimentos dos sistemas DLC ou MoSC. Se estiver particularmente interessado em aumentar a durabilidade das suas ferramentas, pode considerar um dos revestimentos PVD à base de nitretos. Estamos aqui para o aconselhar e conceber uma solução exclusiva para si.
Precisa de aumentar a eficiência e otimizar o seu processo de produção?
Oferecemos consultadoria gratuita para uma solução de revestimento e uma análise custo-benefício.
Somos umas das poucas empresas na República Checa a utilizar a tecnologia HiPIMS (High Power Impulse Magnetron Sputtering – Pulverização catódica de Impulsos de Alta Potência), que é uma variante mais avançada da tecnologia de pulverização catódica. Este processo utiliza impulsos de alta potência para criar plasma com elevada densidade de iões. A tecnologia HiPIMS combina as vantagens do processo de deposição por arco e pulverização catódica permitindo criar revestimentos com microestrutura otimizada, o que significa que os revestimentos podem ser mais lisos, mais densos e ter melhores propriedades mecânicas.
Comparação das tecnologias PVD
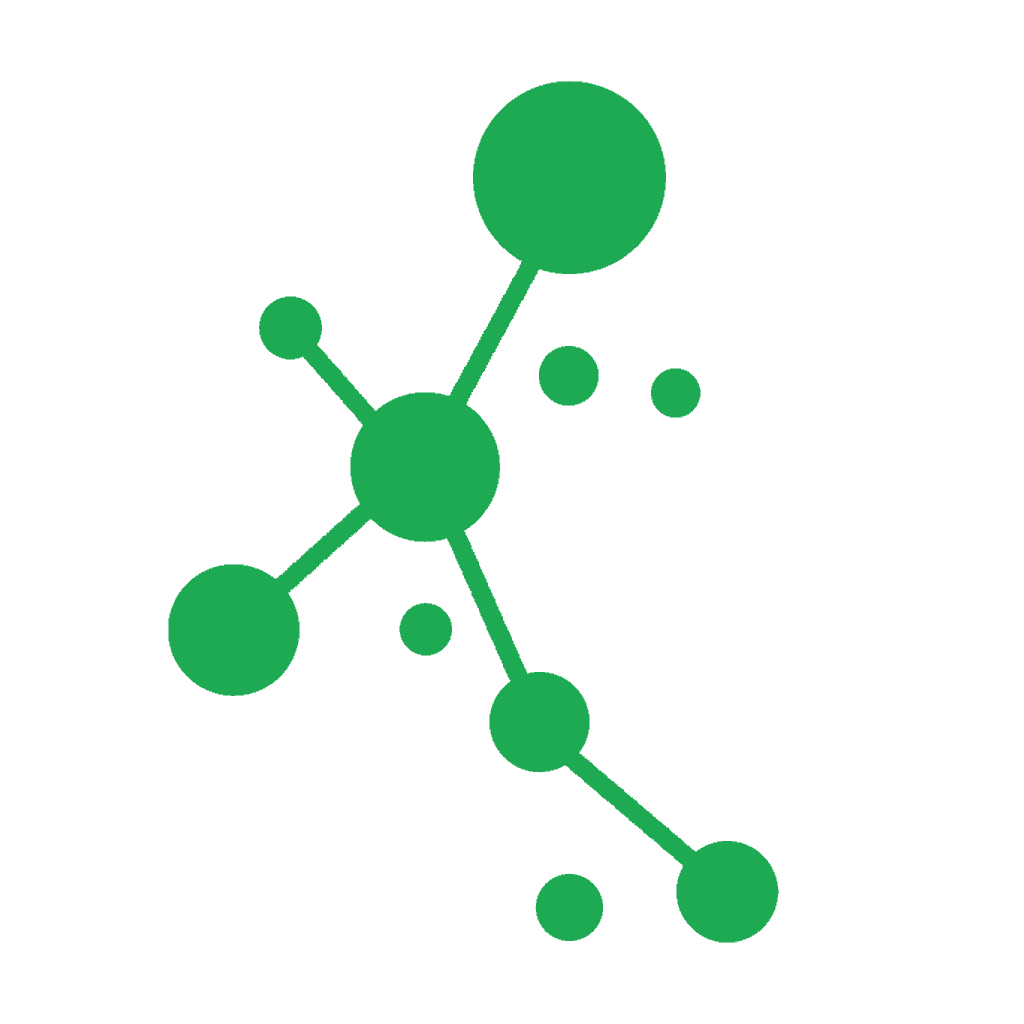
TECNOLOGIA PVD
∴
∴
Vantagens
.
.
Desvantagens
.
.
Produtos típicos
.
.
.
.
.
Motivo de adequação
.
.
.
.
.
.
.
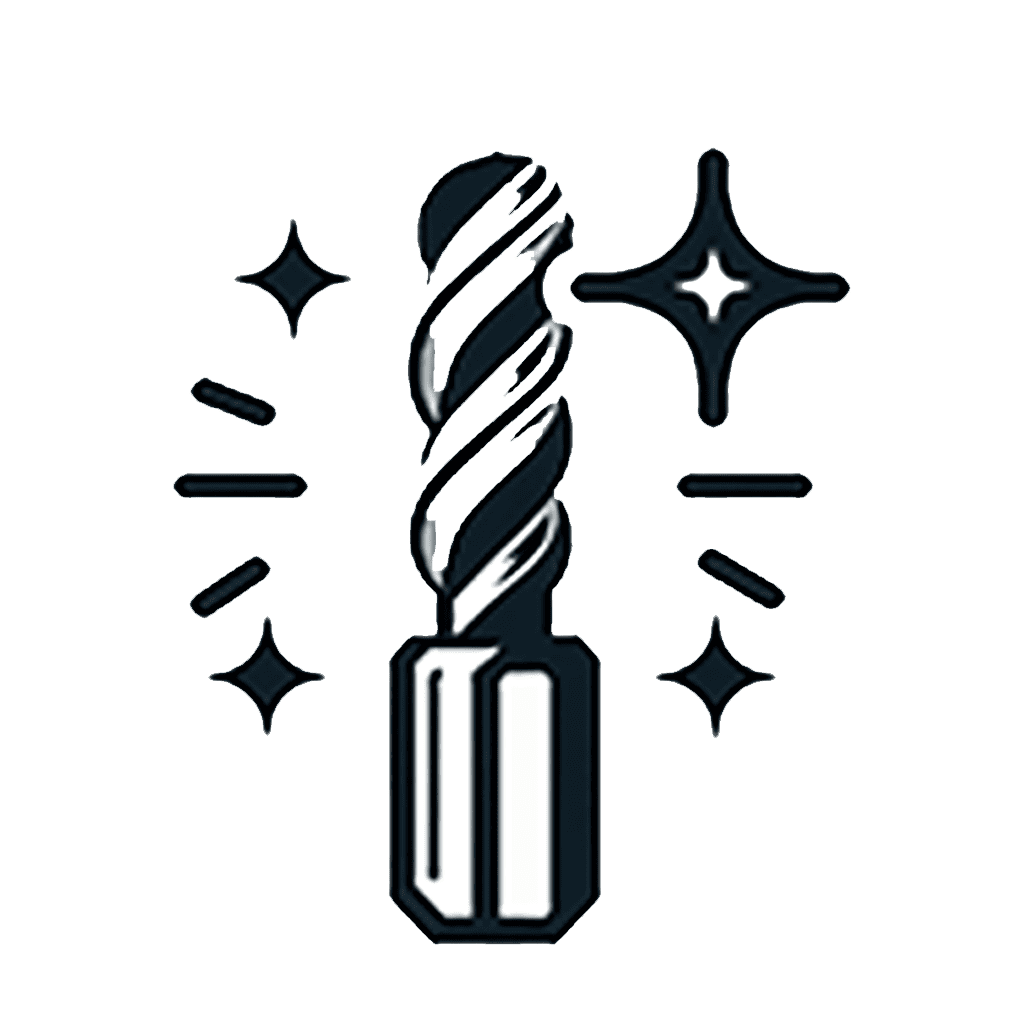
VAPOR ARC
Arc Evaporation
∴
- Maior dureza dos revestimentos
- Elevada aderência e densidade
- Produz gotículas (macropartículas)
- Baixa proteção contra a corrosão
- Tensões internas elevadas
- Ferramentas de corte (brocas, fresas)
- Ferramentas de conformação de metais
.
- Ideal para aplicações que requerem revestimentos muito duros e duradouros, como AlCrN ou AlTiN
- Pode produzir revestimentos com elevada aderência à superfície, o que é fundamental para melhorar a vida útil e o desempenho das ferramentas de corte

PULVERIZAÇÃO CATÓDICA POR MAGNETRÃO
Magnetron Sputtering
- Baixa tensão interna
- Superfície lisa
- Controlo preciso da espessura e da composição do revestimento
- Menor aderência do revestimento em comparação com Arc ou HiPIMS
- Ferramentas de moldagem
- Peças de máquinas em que é necessário um atrito reduzido
- Peças com propriedades ópticas específicas
- Aplicações decorativas
- Permite a produção de revestimentos muito uniformes e homogéneos com uma rugosidade muito baixa em grandes áreas, ideal para a produção de películas finas para ecrãs electrónicos
- Criação de revestimentos extremamente densos e barreiras de difusão
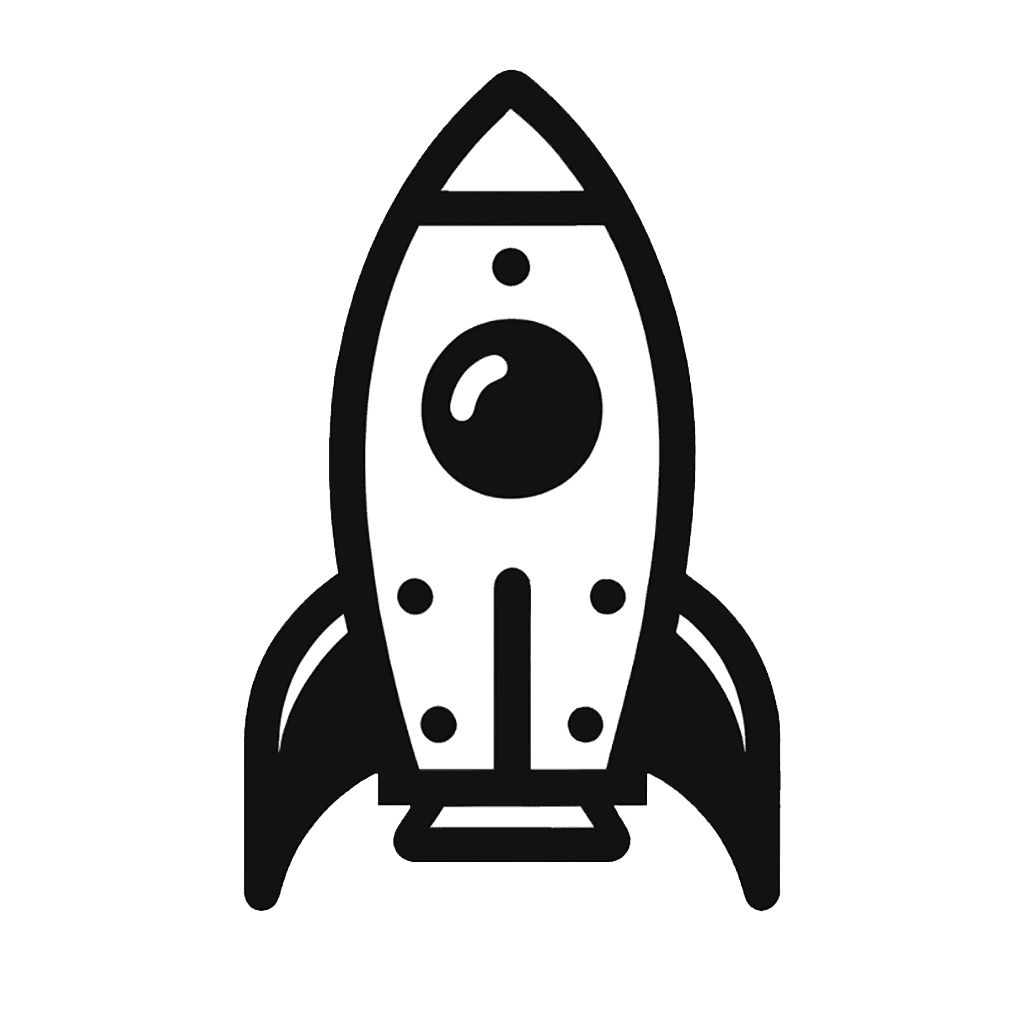
HiPIMS
High Power Impulse Magnetron Sputtering
- Elevada resistência ao desgaste e à corrosão
- Baixas tensões internas
- Superfície lisa sem gotículas
- Elevada dureza dos revestimentos
- Taxa de deposição cerca de 20% inferior
- Ferramentas de corte e conformação
- Componentes aeroespaciais
- Instrumentos e implantes médicos
- Revestimentos decorativos
- Excelentes propriedades de aderência, baixo coeficiente de fricção e elevada resistência à corrosão
- Formação de revestimentos densos e duros
- Excelentes propriedades mecânicas e químicas
Como é que a tecnologia HiPIMS funciona?
HiPIMS significa High Power Impulse Magnetron Sputtering, que se traduz por pulverização catódica de altos impulsos de potência. Ao contrário da pulverização convencional, que pode deixar uma superfície áspera e irregular, a tecnologia HiPIMS devido a ionização de parte do material a depositar permite obter uma superfície mais lisa e um revestimento com boas propriedades mecânicas.
Como é que a tecnologia HiPIMS funciona? Ao contrário da pulverização catódica convencional, a pulverização HiPIMS transfere o material em impulsos de microssegundos com uma potência na ordem dos megawatts. Esta energia é então capaz não só de ionizar os átomos, mas também de implantar esses iões na superfície da peça a revestir. Desta forma, o material revestido liga-se tão bem à peça que é quase como se fossem sempre um só.
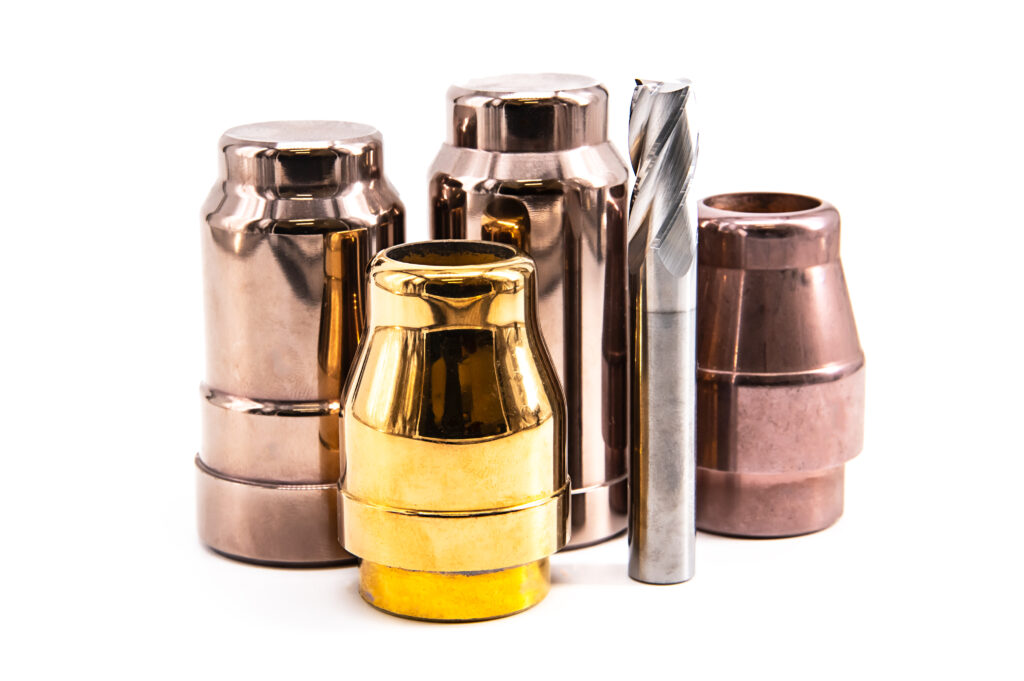
Revestimentos PVD
Os revestimentos PVD são amplamente utilizados numa variedade de indústrias, incluindo ferramentas corte, permitindo prolonga a vida útil, resistência à corrosão e ao desgaste dos componentes. Na indústria eletrónica, permitem melhorar a condutividade e protegem a superfície contra a corrosão, bem como na indústria médica, onde oferecem superfícies biocompatíveis para implantes e instrumentos. Na industria de joelharia e relógios proporcionam acabamentos coloridos únicos e aumentam a resistência aos riscos. Além disso, os revestimentos PVD são mais amigos do ambiente em comparação com alguns processos tradicionais, o que a torna uma escolha ideal para uma vasta gama de aplicações.
Os materiais sintéticos mais duros (HV 1000 - 4000) conhecidos. Elevada resistência à abrasão, ao desgaste e à erosão.
Fina (1 - 10 micrómetros) - impacto mínimo nas dimensões e tolerâncias da peça e ferramentas
A fricção muito baixa (0,01 - 0,6) reduz as perdas por fricção e minimiza o desgaste das peças
Superfícies não adesivas (contra plásticos) - elevada variabilidade de alterações nas propriedades químicas e físicas da superfície
Baixas temperaturas de revestimento (150° - 450°C) - não altera a geometria da peça devido à expansão e mantém a resistência do material
Elevada aderência aos materiais -excelente aderência dos revestimentos a vários materiais - metais, vidro e plásticos
Crescimento do revestimento PVD
O vídeo mostra o crescimento de um revestimento em multicamda Nb e Zr simulado por MD – dinâmica molecular. Na primeira parte do vídeo, as cores representam os átomos de cada elemento. Na segunda parte, as cores mostram o número de átomos vizinhos. O número de átomos adjacentes indicam a estrutura cristalina (bcc para o Nb e fcc para o Zr), bem como os defeitos devidos à sombras e interdifusão.
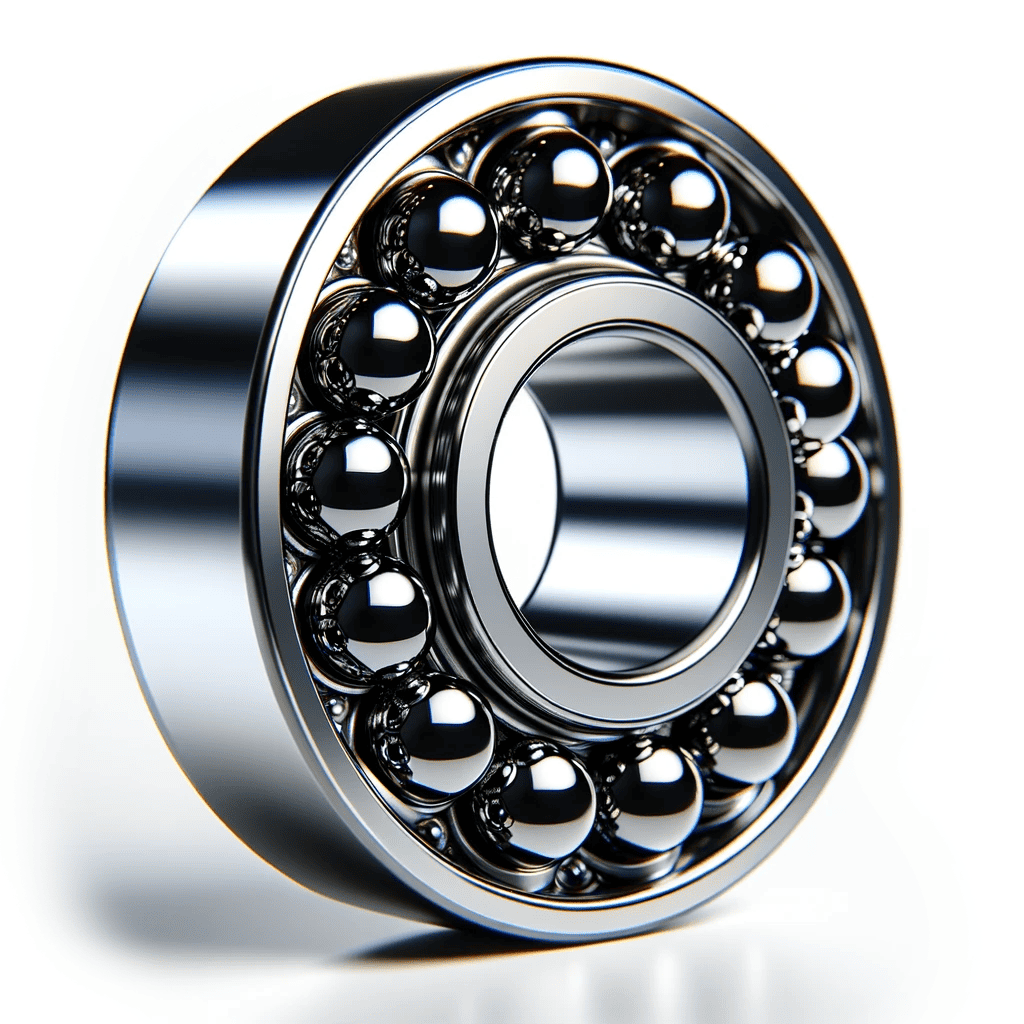
Revestimentos DLC
O DLC "Diamond-Like Carbon" combina algumas das melhores propriedades dos diamantes - a sua incrível dureza e capacidade de resistir a riscos - mas é muito mais económico e flexível na sua aplicação.
Com este revestimento pode proteger qualquer componente, desde peças de automóveis a instrumentos cirúrgicos, até mesmo o seu relógio, conferindo-lhe uma resistência elevada ao desgaste e prolongando a sua vida útil. Para além de tornar o seu material mais durável, os revestimentos DLC também reduzem significativamente o atrito, o que significa que as peças móveis podem mover-se de forma mais suave e eficiente sem sobreaquecer. Isto é ótimo para tudo o que gira, desliza ou se move - desde motores a equipamento de produção e equipamento desportivo.
A nossa especialização
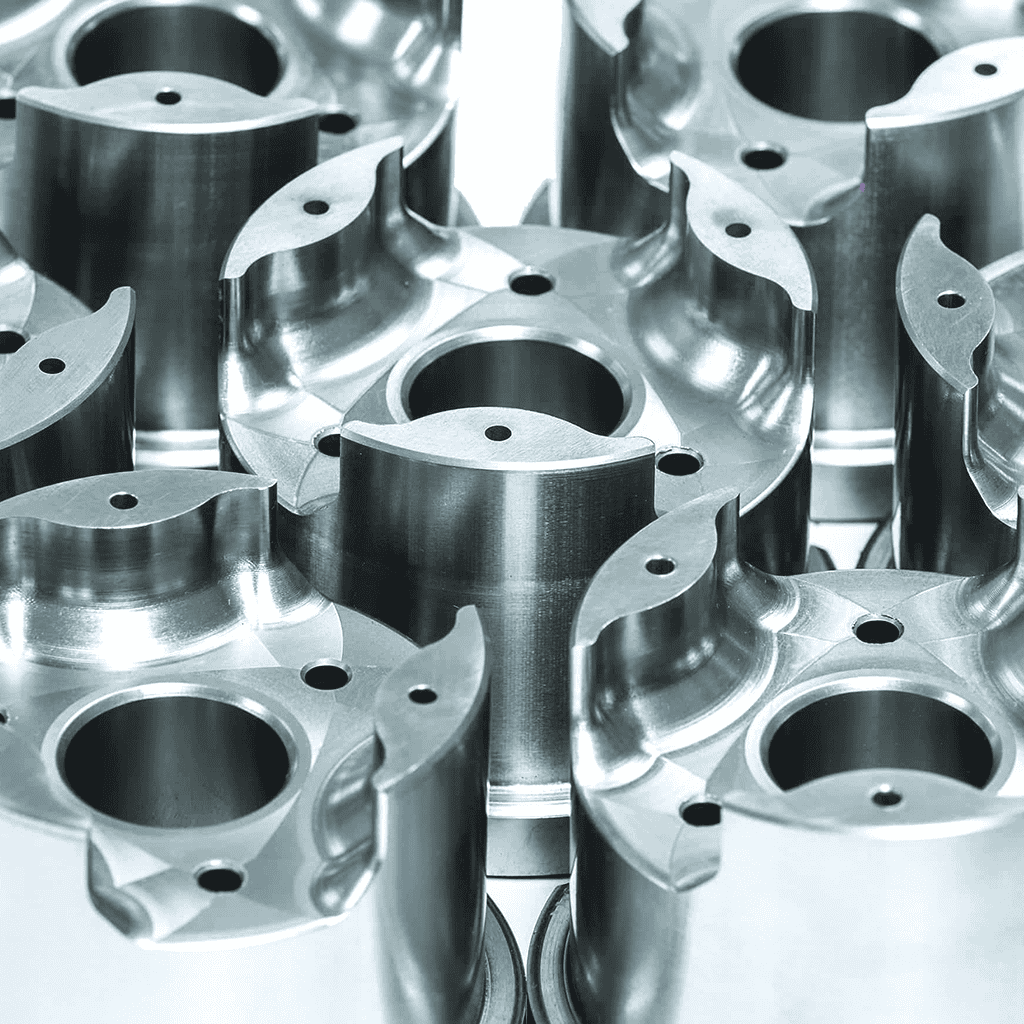
REVESTIMENTO para MOLDES E MATRIZES
Ao contrário de outros processos de PVD, os nossos revestimentos de moldes e matrizes caracterizam-se por uma superfície muito lisa sem pinholas/clusters (normalmente produzidos no processo por arco) e sem estruturas colunares grosseiras (normalmente produzidas por pulverização catódica convencional). Como resultado, é possível obter uma superfície que atinge um desempenho fiável e uma eficiência ótima.
O revestimento de ferramentas para conformação permite prolongar a sua vida útil, reduzindo assim os custos de produção. O revestimento adequado evita o desgaste abrasivo (por exemplo, em plásticos compostos de fibra de vidro), o desgaste adesivo e a desmoldação em peças com formas complexas.
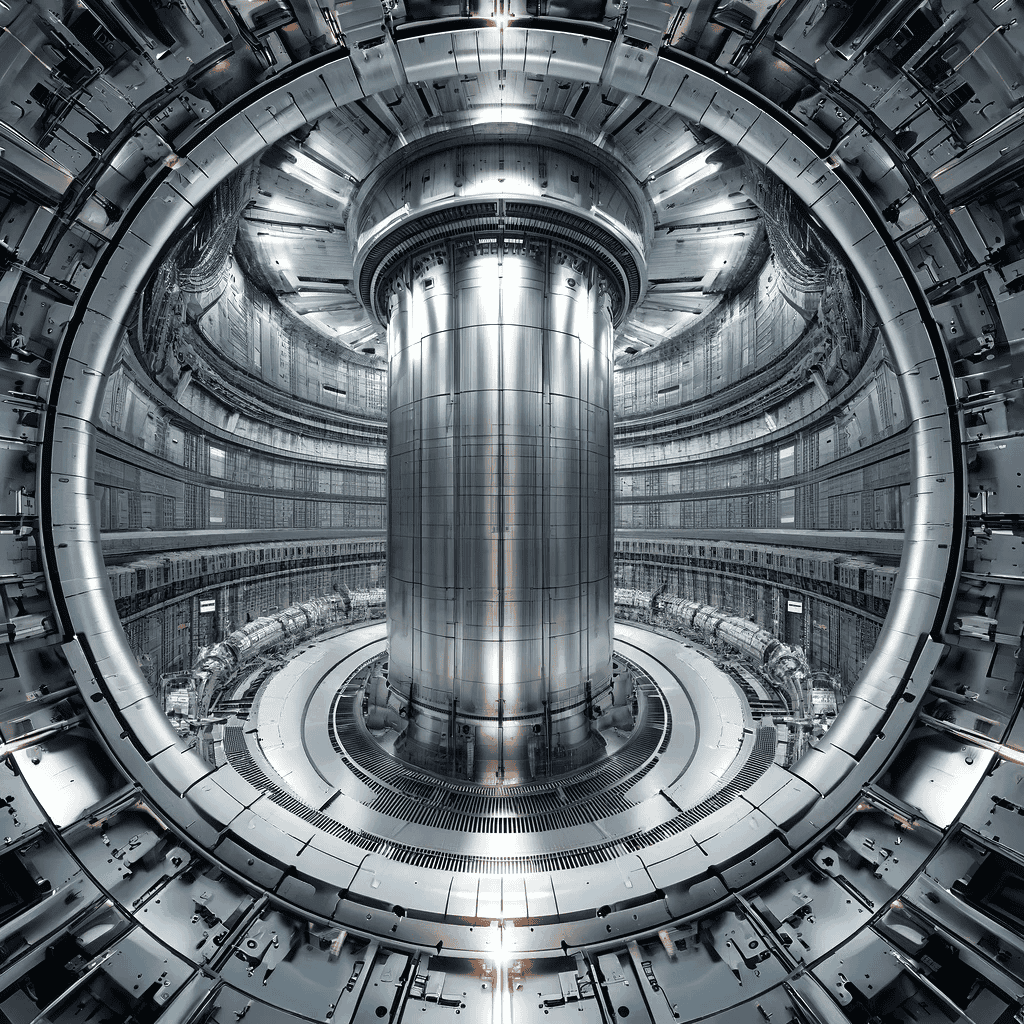
REVESTIMENTOS PARA TOKAMAKS E DISPOSITIVOS DE FUSÃO
Desenvolvemos tecnologia de revestimento para utilização em fusão nuclear e experiências científicas avançadas. Os nossos serviços incluem a aplicação de revestimentos de tungsténio, molibdénio, crómio e zircónio especificamente concebidos para Tokamaks. Utilizando métodos de vanguarda, conseguimos aplicar camadas até 20 microns de espessura, o que é ideal para equipamento que requer resistência máxima a temperaturas extremas e ambientes corrosivos típicos de experiências de fusão nuclear. Esta tecnologia não só aumenta a eficiência e a durabilidade dos componentes, como também contribui significativamente para a segurança de todo o sistema. Oferecemos consultoria individual e personalização da tecnologia de acordo com as suas necessidades específicas e especificações do projeto.
REVESTIMENTOS resistentes ao desgaste - DLC, WS2, WSC/WSN
Os revestimentos resistentes ao desgaste são utilizados sempre que é necessário reduzir o coeficiente de atrito, prevenir gripagem das peças e assegurar boas propriedades autolubrificantes na ausência de liquidos lubrificantes
O princípio básico dos revestimentos anti-desgaste é a formação de uma camada de transferência, que é formada no contacto entre os materiais. Um exemplo comum são os revestimentos DLC. Os revestimentos DLC no estado depositado são constituídos por carbono com ligações sp3, típicas do diamante e ligações sp2 típicas da grafite (aproximadamente 50:50). A ligação típica do diamante proporciona uma elevada dureza e grafite proporciona um baixo atrito. A presença de grafite no contacto permite baixar o atrito e, consequentemente, diminuir o desgaste.
Os nossos revestimentos WSC/WSN baseados em dicalcogenetos de metais de transição funcionam segundo um princípio semelhante. No entanto deve ser realçado que no topo da superfície do revestimento há alinhamento dos planos do revestimento.
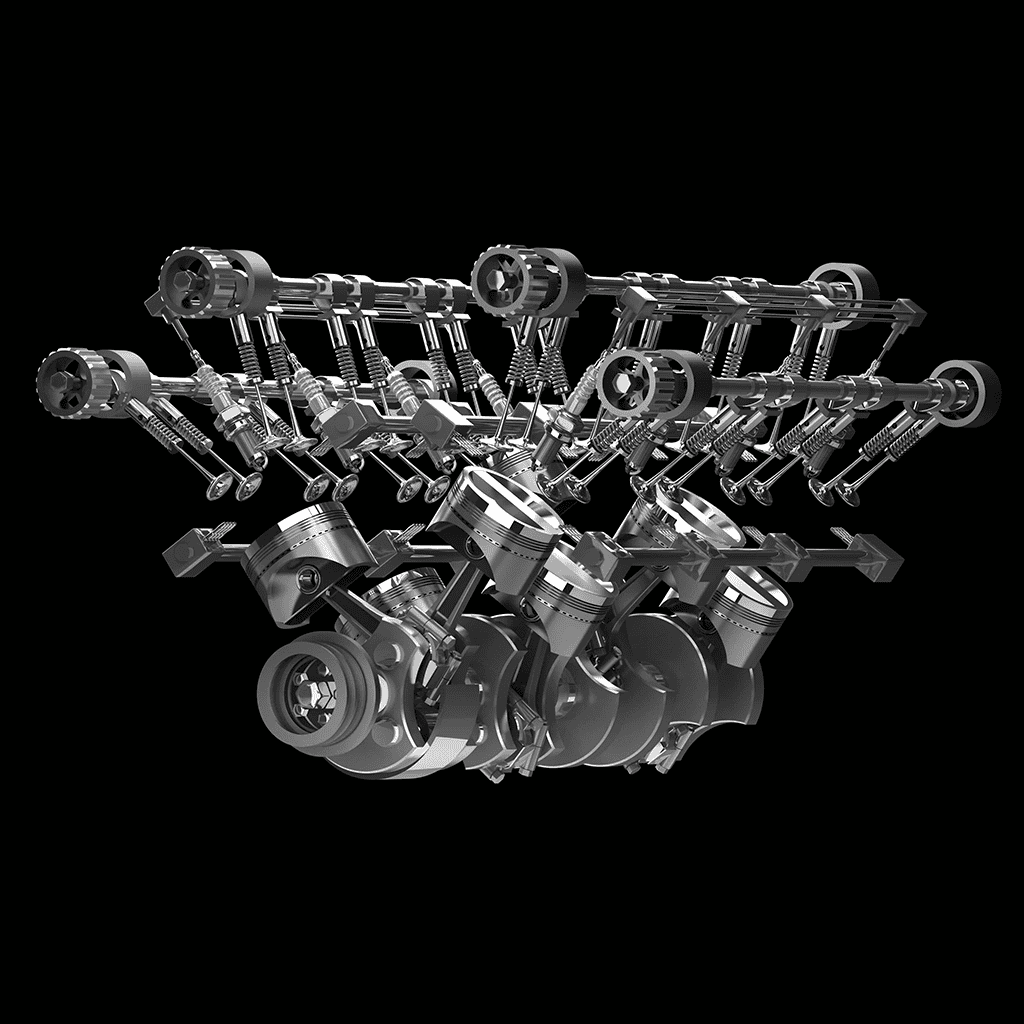
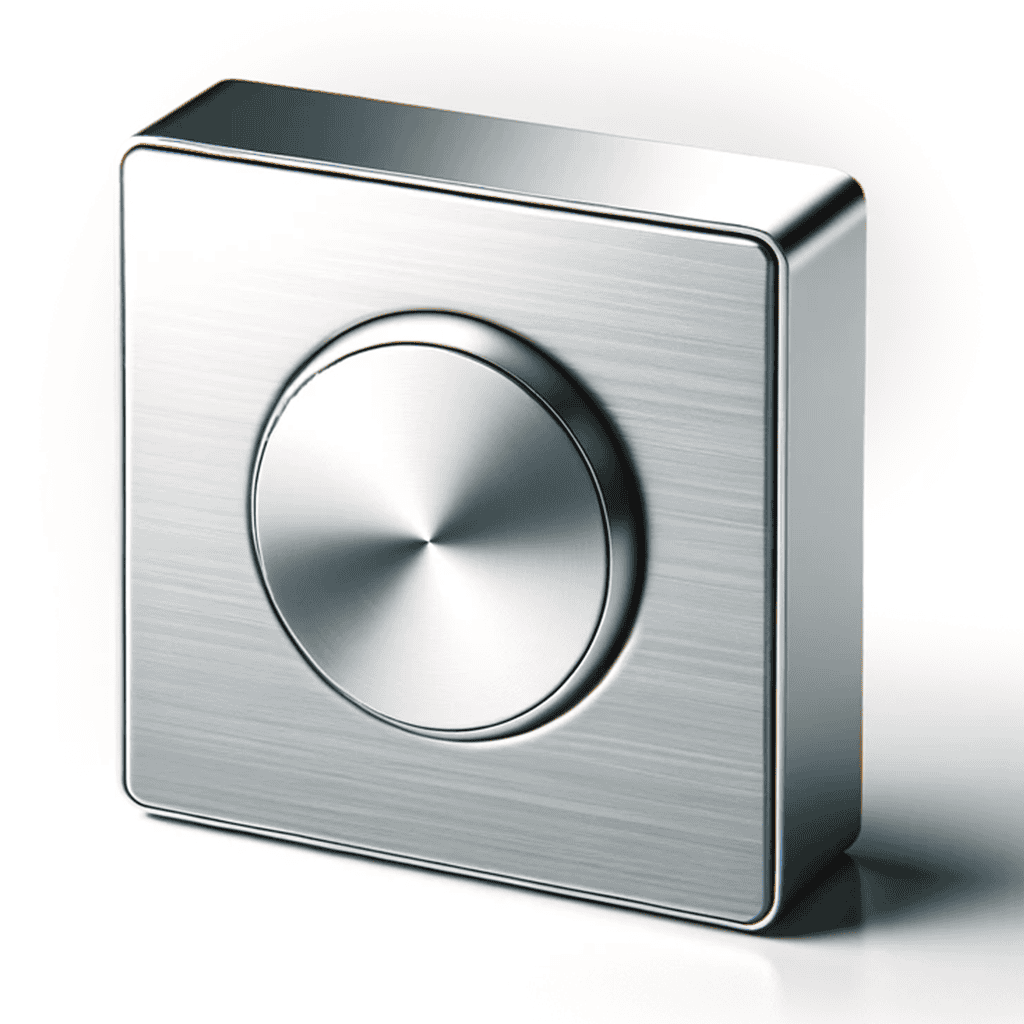
Revestimento em plásticos
Graças a uma tecnologia especial desenvolvida pela nossa empresa, é possível revestir peças de plástico em pequenas e grandes séries com revestimentos metálicos decorativos com cor de ouro, prata e bronze.
Durante a deposição as peças de plástico são submetidas a temperaturas baixas, T<50°C, pelo que mesmo peças com paredes finas não são afectadas. Todos os materiais poliméricos que possam ser sujeitos a condições de vácuo: ABS, PP, PE, PA ou PEEK, podem ser revestidos. O tamanho máximo da peça possivel de revestir é de 1500 x 1500 x 300 mm.
Este processo de revestimento é amigo do ambiente, substitui o crómio duro obtido por electrodeposição e está de acordo com a legislação REACH.
Revestimento a baixas temperaturas
Aplicamos revestimentos duros de nitreto e metálicos a baixas temperaturas, < 150°C. Graças a fontes pulsadas, conseguimos obter revestimentos muito duros com uma adesão perfeita, mesmo a temperaturas baixas.
Podemos revestir aço 19 312, aços nitretados, ligas de alumínio e materiais que posaam alterar as suas propriedades com a temperatura. A baixas temperaturas, depositamos principalmente CrN, TiN, TiAlN, (CrAl)203 e DLC, podendo ser seleccionados outros materiais.
Também podemos revestir plásticos e peças obridas por fabrico aditivo (PLA, ABS e outros). Nestes casos, os revestimentos apenas servem para dar propriedades decorativas ou para melhorar a condutividade eléctrica.
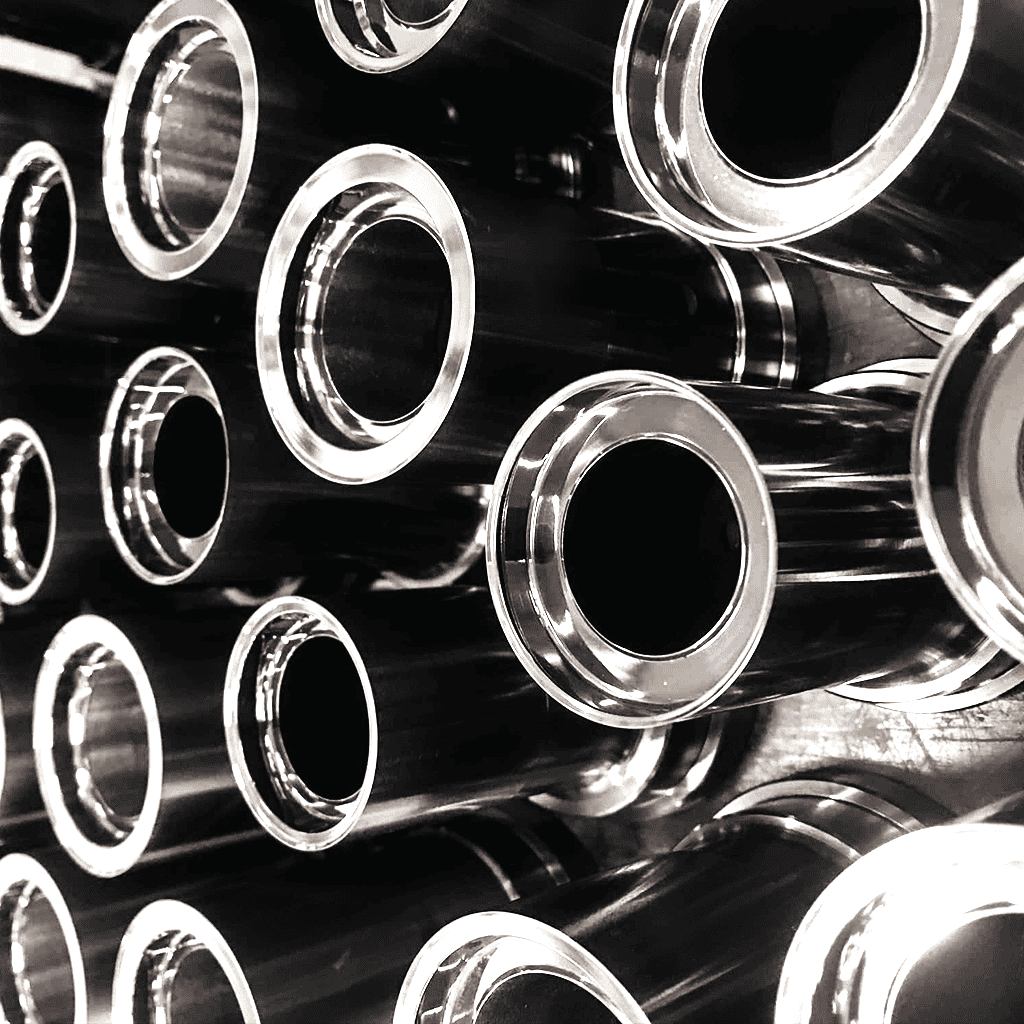
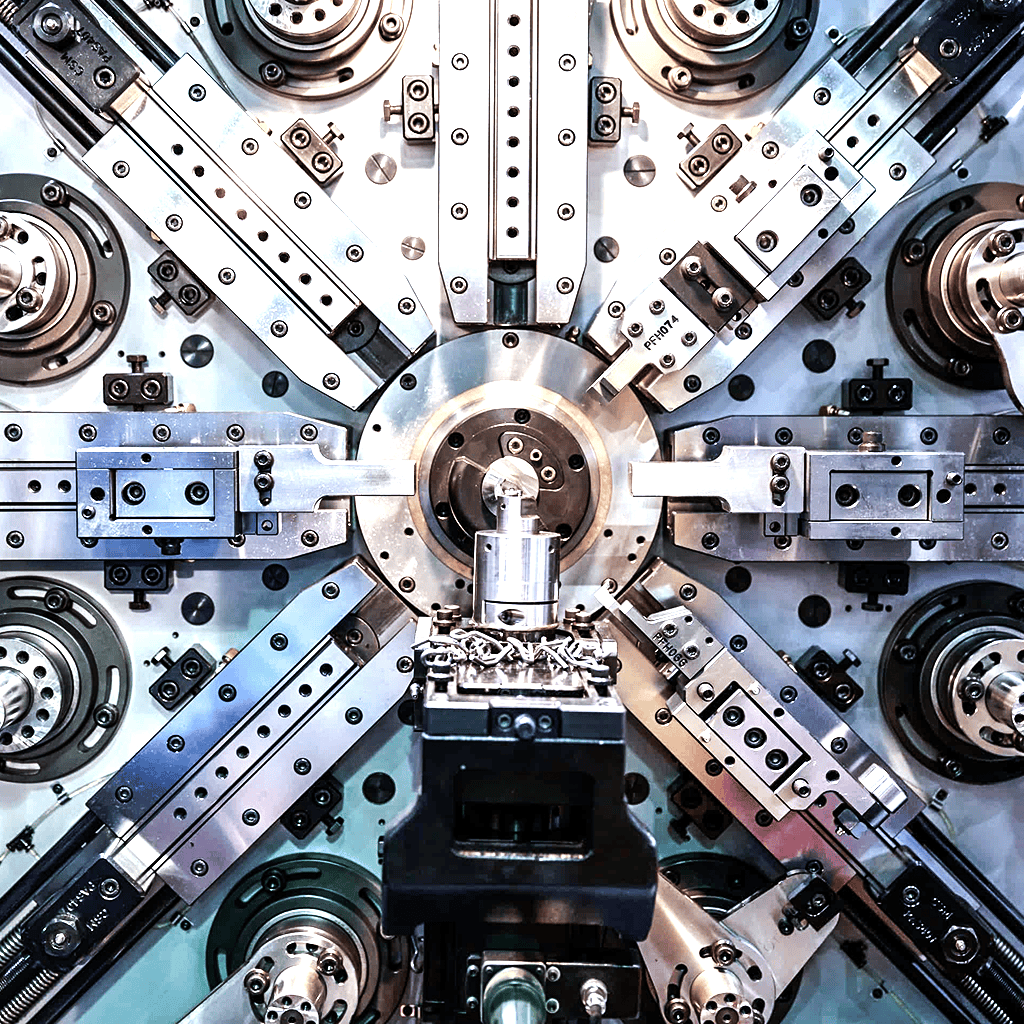
Otimização dos seus revestimentos
A AdvaMat Lda. concentra-se principalmente no desenvolvimento e otimização de revestimentos, para que estes façam face às necessidades do cliente. Para otimizar o revestimento de forma rápida e económica, utilizamos não só métodos de tentativa e erro, mas também um vasto equipamento de medição. Para além das propriedades mecânicas habituais dos revestimentos, podemos medir e ajustar as tensões residuais do revestimento, avaliar o atrito do revestimento contra qualquer material (de acordo com as normas ISO e ANSI) medir a rugosidade e a geometria da superfície com grande precisão (por exemplo, após retificação ou polimento de lâminas, etc.).
Revestimento de ligas de alumínio
O revestimento de componentes e ferramentas produzidas em ligas de alumínio demonstra claramente a importancia do revestimento. As ligas de alumínio permitem fabricar componentes mais leves, são normalmente fáceis de maquinar, no entanto necessitam de ser revestidas para aumentar dureza e outras propriedades importantes.
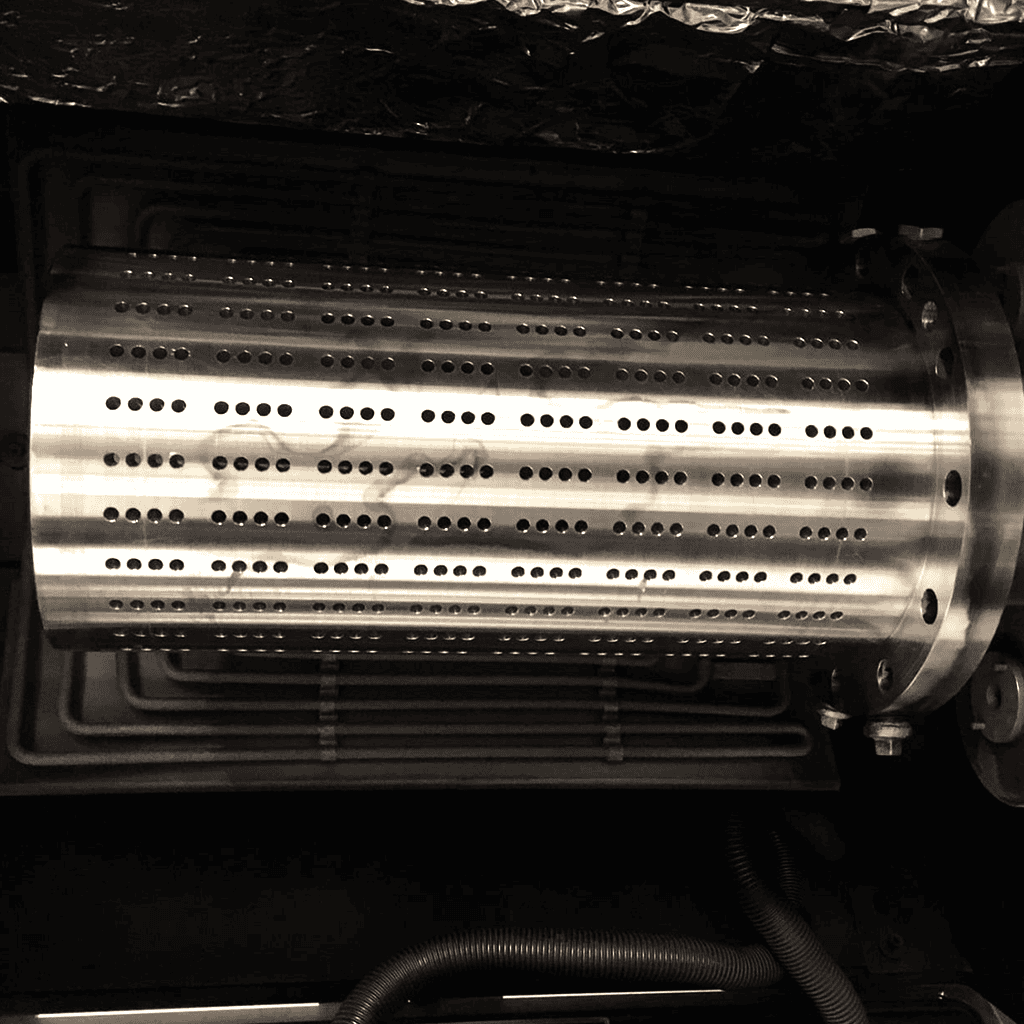
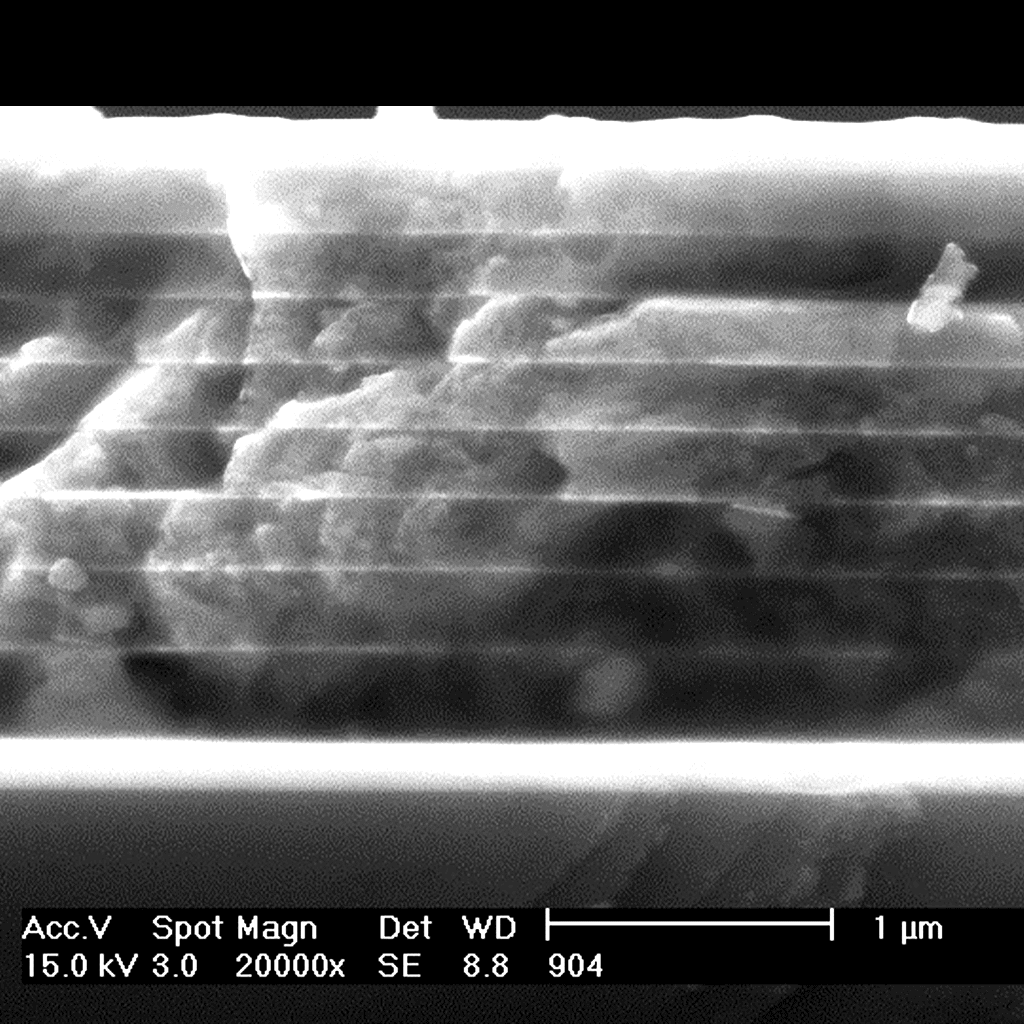
Revestimentos isoladores
Os nossas revestimentos PVD não condutores são principalmente os revestimentos DLC e os revestimentos à base de óxidos. Os revestimentos DLC são usados em aplicações tribológicos para reduzir o atrito,em aplicações onde a corrosão é importante e como revestimentos decorativos de artigos de luxo.
Os revestimentos à base de óxidos não foram aplicados em ferramentas e componentes da indústria durante muitos anos, devido à sua dificuldade de deposição. Estes materiais quando depositados criam camadas isoladoras electricas no alvos de deposição e tornam o processo de revestimento instável e/ou mesmo impossível. A deposição deste tipo de materiais necessitam de equipamentos de controlo especiais.
Os revestimentos à base de óxidos (Al2O3, (AlCr)2O3 e Cr2O3) são ótimos para resistir à oxidação a altas temperaturas, evitar a adesão dde plásticos, ligas de alumínio e outros metais.